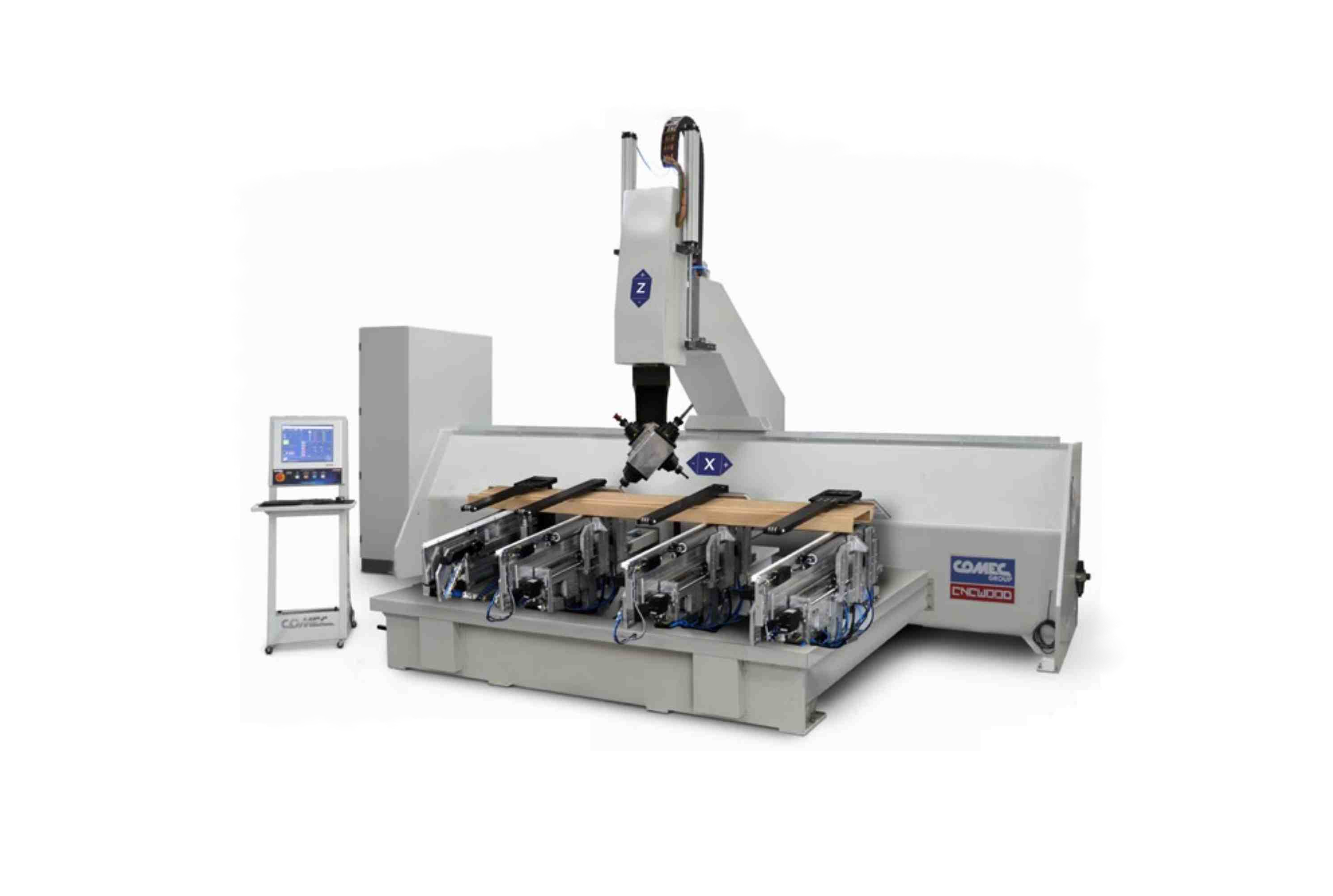
This video will be loaded from Google YouTube.
Their
privacy policy applies.
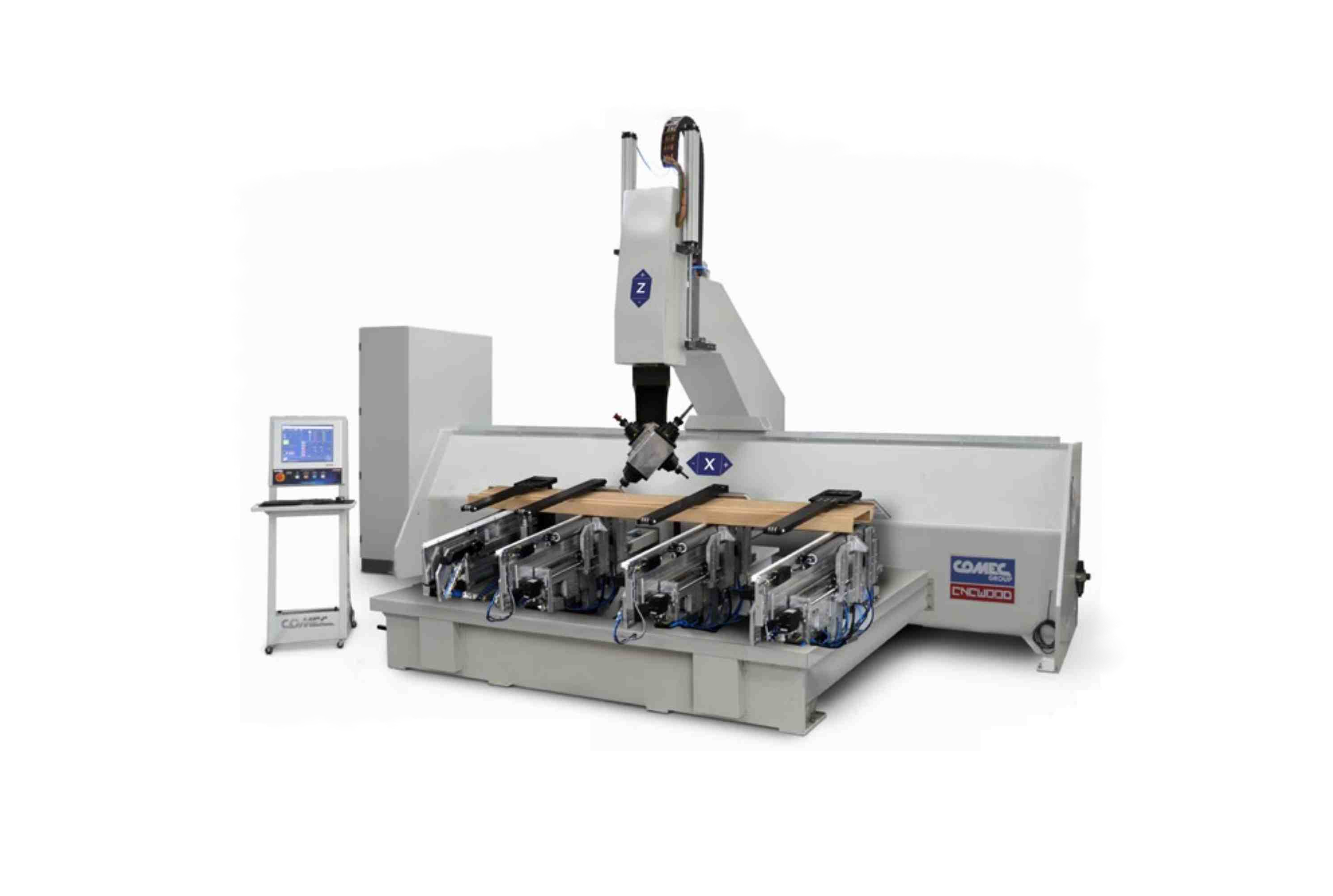
luD8-wMGCQY
BrandCOMEC
typeVariax J
stateNew
stock number1110195
The highest level of progress for your door frame production:
- The Variax J is characterized by 6 controlled axes and a fast manufacturing process.
Questions about this machine
CNC working center
Brand: Comec
Type: Variax J
new machine
The highest level of progress for your door frame production: 6 controlled axes and a fast production process characterize the Variax J.
Movable machining support
- All axes move on ball bearing mounted BOSCH-REXROTH or comparable linear guides
- Movement / positioning of the machining units max. 70 m/min.
- Axis X = 2950 mm
- Axis Y = 400 mm
- Axis Z = 500 mm
- Axis support for vertical rotation of the machining head.
axis B from -135° to +135°, motor kW 0.45.
- Axis support for horizontal rotation of the machining head.
Axis C from -180° to +180°, motor kW 0.45.
Machining head - electrospindle 1-2
- N°1+1 electrospindle fixed to the "H" support
- N°1 electrospindle for milling,
- with 2 spindle outputs, kW 7.0 / 12-18.000 rpm, adjustable by means of frequency converter Tool attachment with union nut and collet ER 32
Machining head - electrospindle 3-4-5
- N°1+1 electrospindle fixed to the "H" support.
- N°1 electrospindle for milling / sawing, with 2 outputs, kW 4.0 / 4-6.000 rpm, adjustable by means of frequency converter.
Tooling 3,4 and 5.
- W 3. saw blade Ø 250 mm.
- W 4. N°1 drill output. Receptacle Ø 10 mm
- W 5. N°1 drill head with 2 outputs at 180°, receptacle Ø10 mm.
Machining head electrospindle 6
- N°1 electrospindle fixed to the back of the machining support.
Equipped with support for horizontal rotation from -180° to +180°, axis C, motor kW 0.45.
- N°1 electric spindle for drilling/milling, kW 1.8 / 8.000-12.000 rpm, adjustable by means of frequency converter.
Special underfloor gear for machining the workpiece on the inside from below.
Tool holder collet ER 20 mini. For special drilling tool Ø 35 mm.
Workpiece clamping table
N°1 workpiece clamping table with:
B1
N°4 workpiece clamping benches adjustable on guides with ball bearings,
manual clamping, releasing and positioning in X-direction, reading on millimeter scale.
Each bench is equipped with:
B2
N°1 Solid and compact reference fence 90 degrees °, with additional pivoting locking arm to lock the workpiece fence to prevent any movement.
B3
N°1 front workpiece stop with clamping cylinder, via spindle and servomotor with programmable position, set-up Y1 axis.
Needed to hold the mounted trim at 90 degrees to the chuck.
N°1 front workpiece stop with clamping cylinder, m onted on the back side.
B4
N°1 vertical clamping cylinder manually adjustable, Y2 axis, on the front.
N°1 vertical clamping cylinder mounted on the back.
B5
N°1 workpiece support rail to position the frames against the workpiece stop in the simplest and most ergonomic way, manually adjustable in height Z axis.
Safety devices
- Safety protection booth with side entrance door.
N°1 synchronized transparent polycarbonate safety curtain for an optimal view of the machining area. 2-hand start button for the start of the machining operation.
Control unit
Self standing control unit placed on the left side of the machine.
Numerical control specially designed as a control unit for NC axes and the various functions / operations for multi-axis milling / drilling machines.
Industry PC as operator interface with 17" color screen.
Hard disk SSD: 120 GB Network: Ethernet/USB/RS232
Operating system Windows 10 EMB multilingual.
DDX SOFTWARE Parametric programming supported by 3D workpiece and machining modeling.
3D workpiece display with representation of machining steps.
Complete with traverse optimization and associated post-processor.
Network connection possible for programming and remote service support
Remote console for machine testing and operator adjustment.
Optionally available against surcharge:
A - workpiece clamping table CNC -
N°1 Workpiece clamping table
B1
N°4 Clamping benches adjustable on linear guides with ball bearings. Automatic clamping/releasing, NC controlled by the moving support equipped with corresponding pincers. This grips the bench and moves it in position in X direction as stored in the program.
Each bench equipped with:
B2
N°1 Solid and compact reference fence 90 degrees °, with additional pivoting locking arm to lock the workpiece fence to prevent any movement.
B3
N°1 front workpiece stop with clamping cylinder, over spindle and servo motor with programmable position, set-up Y1 axis. Needed to keep the mounted trim 90 degrees to the chuck. N°1 front workpiece stop with clamping cylinder, mounted on the rear side.
B4
N°1 vertical clamping cylinder automatically adjustable by the machining head, through NC program, Y2 axis, on the front side. N°1 vertical clamping cylinder mounted on the back.
B5
N°1 workpiece support rail to position the frames easily and ergonomically against the workpiece stop, automatically adjustable in height Z axis, by the machining head, via NC program.
B - Laser sensor
Laser sensor integrated in the machining head
Automatically detects any small difference in the thickness of the workpiece in order to have the machine accurately adjusted at any time with respect to the zero point
C - Bar code reader
Bar code reader, for program call from the machining list Software upgrade for program call by reader Works with bar code and QR code
D - Chip conveyor
N°1 Chip conveyor, 4.000 x 1.000 x 100 H mm
E - Upgrade safety / protection cabin
Safety cabin, complete with roof.
(Recommended for the processing of MDF - materials).
F - Installation and commissioning
5 working days with 2 technicians for installation, commissioning and training of operators.
- Overnight stay and expenses exclusive.
Contact person
Eugen Pries
Sales East Europe & Asia
Ralf Teubner
Sales Swiss & International
Richard Brakweh
Sales Belgium, Netherlands, Luxembourg & Scandinavia